A Guide to Selecting Materials for CNC Machining Projects
Introduction: CNC machining is the backbone of various industries, from aerospace to electronics, offering unparalleled precision in creating machined parts. Choosing the right materials is crucial for optimal component performance and durability in demanding applications. This guide explores the world of CNC materials, providing insights into their properties and applications, aiming to enhance your understanding without overwhelming you with excessive details.
Factors to Consider when Choosing CNC Machining Materials:
-
Machining Environment:
- Consider the impact of temperature, humidity, and contaminants on materials.
- Some materials may chip or crack at high temperatures, while others may experience tool wear.
- Compatibility with coolants or lubricants is crucial to prevent damage during machining.
-
Part Weight:
- Evaluate the weight of parts for cost-effectiveness, performance, and manufacturability.
- Lighter materials like aluminum or magnesium reduce production costs and may enhance fuel efficiency in applications like aerospace or automotive.
-
Heat Resistance:
- Select materials based on their ability to withstand high temperatures without deformation.
- Metals like aluminum and copper are suitable for heat sinks, while stainless steel and titanium excel in aerospace and medical applications.
-
Electrical Conductivity and Magnetic Requirements:
- Consider materials' electrical conductivity for efficient heat dissipation.
- Non-magnetic options like titanium and stainless steel are preferable in CNC machining to avoid interference from magnetic fields.
-
Hardness:
- Opt for materials with the right hardness for ease of machining and high-quality results.
- Balance hardness to prevent excessive tool wear or deformation during cutting.
-
Surface Finish:
- Surface finish impacts performance, with smoother finishes reducing friction and enhancing aesthetics.
- Consider material machinability for achieving the desired surface finish, with metals like aluminum and brass known for easy machining.
-
Aesthetics:
- In high-end retail products or industries like automotive and aerospace, aesthetics play a crucial role.
- Choose materials that offer visual appeal and allow for easy polishing, painting, or finishing.
-
Application:
- Tailor material selection based on specific application requirements, considering machinability, chemical stability, adhesive properties, and fatigue resistance.
-
Budget:
- Establish a budget considering material costs and CNC machining expenses.
- Balance cost-effectiveness with the need for high-quality, durable materials to ensure the final product meets standards.
Best Materials for CNC Machining Projects:
Metal CNC Materials:
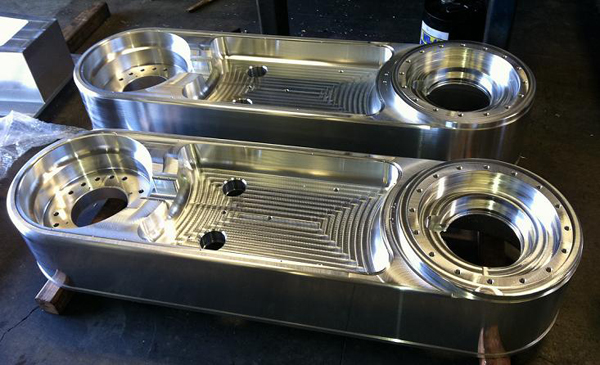
- Aluminum (6061, 7075): Lightweight, corrosion-resistant, ideal for aerospace and automotive applications.
- Stainless Steel (316, 303, 304): High strength, wear resistance, suitable for marine and medical applications.
- Carbon Steel and Alloy Steel: Excellent strength, machinability, and affordability for various applications.
- Brass: Excellent machinability, corrosion resistance, and aesthetic appeal for consumer products.
- Copper: High electrical and thermal conductivity, suitable for electronic applications.

Plastic CNC Materials:
- Acetal (POM): Versatile, excellent fatigue resistance, suitable for precision components.
- Acrylic (PMMA): Good rigidity, optical clarity, used in transparent enclosures and decorative items.
- Polycarbonate (PC): Highly transparent, heat-resistant, ideal for safety glasses and electronic displays.
- Polypropylene (PP): High chemical resistance, fatigue strength, suitable for gear and medical products.
- ABS: Cost-effective, machinable, used in automotive components and rapid prototyping.
- Nylon: Excellent tensile strength, impact resistance, suitable for gears and sliding surfaces.
- UHMW-PE: High hardness, abrasion resistance, ideal for sliding surfaces in bearings and gears.
Other Materials:
- Foam: Lightweight with air-filled voids, suitable for protective packaging and decorative items.
- Wood: Easy to machine, offers good strength and hardness, popular for furniture and DIY projects.
- Composites: Carbon fiber, plywood, and fiberglass offer versatility in various industries, though machining can be challenging.
Considerations Beyond Conventional Materials:
- Explore non-metallic materials as equal substitutes for metals.
- Consider cost-effective phenolics with high rigidity for machining at high speeds.
- Understand the diverse portfolio of CNC plastics, offering a range of material properties.
- Explore different foams with potential applications in CNC machining projects.
Conclusion: Designing for manufacturing requires careful consideration of materials, and with advancements in material science, CNC machining offers a wide array of options. Our expertise in CNC machining services ensures precision and quality across various materials, from metals to plastics. Explore the possibilities and make informed decisions to achieve success in your CNC machining projects.
Ningbo Fuerd was founded in 1987 and is a leading full-service die-casting tooling, aluminum die casting, zinc die casting, and gravity casting manufacturer. We are a solution provider offering various capabilities and services that include engineering support, designing, molds, complex CNC machining, impregnation, tumbling, chrome, powder coating, polishing, assembly, and other finishing services. We will work with you as partners, not just suppliers.