Aluminum Squeeze Casting vs. Aluminum Die Casting
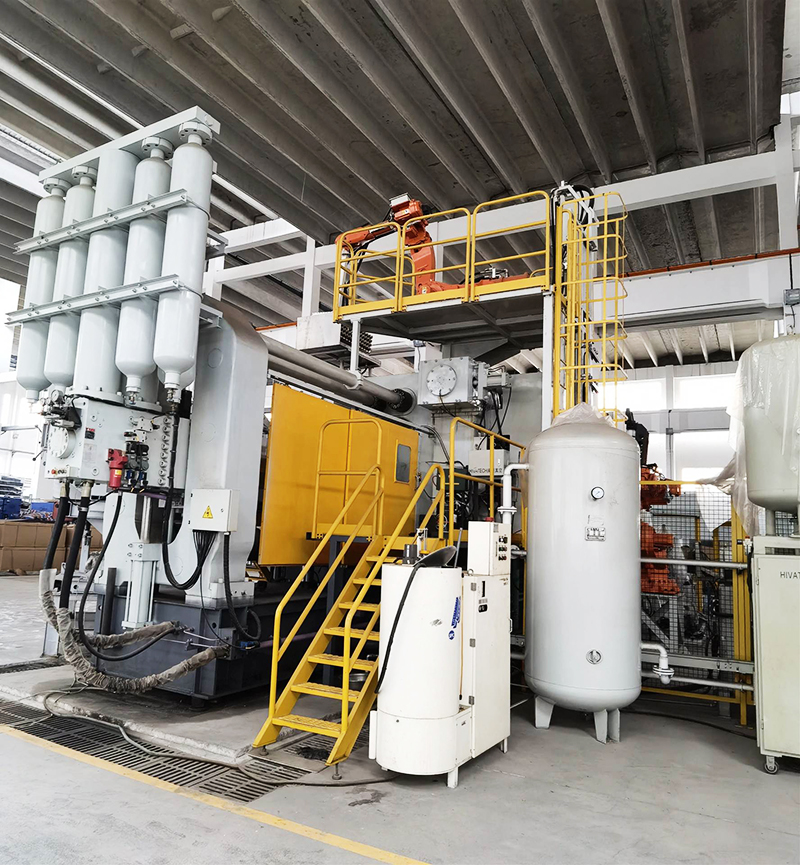
Both aluminum squeeze casting and aluminum die casting are effective methods for producing aluminum parts. They have distinct differences in processes, advantages, disadvantages, and specific applications.
1. Process Overview
-
Process Steps:
- Mold Preparation: A mold is created, often made of steel, designed to withstand high pressure.
- Pouring: Molten aluminum is poured into the mold cavity.
- Application of Pressure: A hydraulic press applies pressure (typically 1,000 to 3,000 psi) to the molten metal, forcing it to fill the mold completely.
- Cooling: The part cools under pressure, minimizing defects like porosity.
- Ejection: Once cooled, the part is removed from the mold.
-
Key Features:
- Higher pressure leads to better filling of intricate mold designs and reduced voids.
-
Process Steps:
- Mold Creation: Two-part molds (die) are machined with precision.
- Injection: Molten aluminum is injected into the die under high pressure (up to 10,000 psi).
- Cooling: The metal solidifies quickly within the die.
- Ejection: The die opens, and the finished part is ejected.
-
Key Features:
- Fast cycle times allow for high-volume production, often within seconds.
2. Material Properties
Squeeze Casting
- Mechanical Properties:
- Produces components with higher tensile strength, fatigue resistance, and toughness due to the dense microstructure.
- Porosity:
- Significantly reduced compared to die casting, resulting in parts that can withstand higher stresses.
- Surface Finish:
- Generally smoother, which may reduce or eliminate the need for secondary finishing processes.
Die Casting
- Mechanical Properties:
- Good but often lower than squeeze-cast components due to some porosity and microstructural differences.
- Porosity:
- Can exhibit porosity, particularly in complex shapes, but modern techniques can mitigate this.
- Surface Finish:
- High-quality surface finishes are achievable, suitable for decorative applications without extensive machining.
3. Advantages and Disadvantages
Aluminum Squeeze Casting
Advantages:
- Excellent mechanical properties and strength.
- Lower porosity leads to higher reliability in critical applications.
- Capable of producing large, complex shapes with high dimensional accuracy.
Disadvantages:
- Slower production rates make it less suitable for high-volume manufacturing.
- Higher tooling and setup costs due to specialized molds and equipment.
Aluminum Die Casting
Advantages:
- Very high production rates; ideal for mass production.
- Lower per-unit costs when producing large quantities.
- Good dimensional accuracy and surface finish.
Disadvantages:
- Can have more porosity and lower mechanical properties compared to squeeze casting.
- Limited to less complex shapes due to filling limitations under high pressure.
4. Applications
Squeeze Casting Applications:
- Automotive Parts: Engine blocks, suspension components, and other high-strength parts that require durability and reliability.
- Aerospace Components: Structural components that need to withstand extreme conditions and stresses.
- Industrial Machinery: Parts that require high precision and strength, such as frames and housings.
Die Casting Applications:
- Consumer Electronics: Housings and frames for devices, including phones and computers.
- Automotive Components: Brackets, housings, and intricate parts used in engines and transmissions.
- Home Appliances: Components such as casings for washing machines and dryers.
5. Environmental Considerations
- Squeeze Casting: Generally produces less waste material as the process can utilize almost all of the molten aluminum.
- Die Casting: Can generate more waste due to excess material during the injection process, though recycling systems can mitigate this.
Summary
In conclusion, the choice between aluminum squeeze casting and aluminum die casting hinges on specific project requirements, including mechanical properties, production volume, cost, and part complexity. Squeeze casting is ideal for applications demanding high strength and low porosity, while die casting is preferred for large-scale production of intricate parts at lower costs. Understanding these differences can help manufacturers select the best method for their needs.
Ningbo Fuerd was founded in 1987 and is a leading full-service die Casting Tooling, aluminum die casting, zinc die casting, and gravity casting manufacturer. We are a solution provider offering a wide array of capabilities and services that include engineering support, designing, molds, complex CNC machining, impregnation, tumbling, chrome, powder coating, polishing, assembly, and other finishing services. We will work with you as partners, not just suppliers.