How Die Castings Empower the Mass Production of Humanoid Robots?
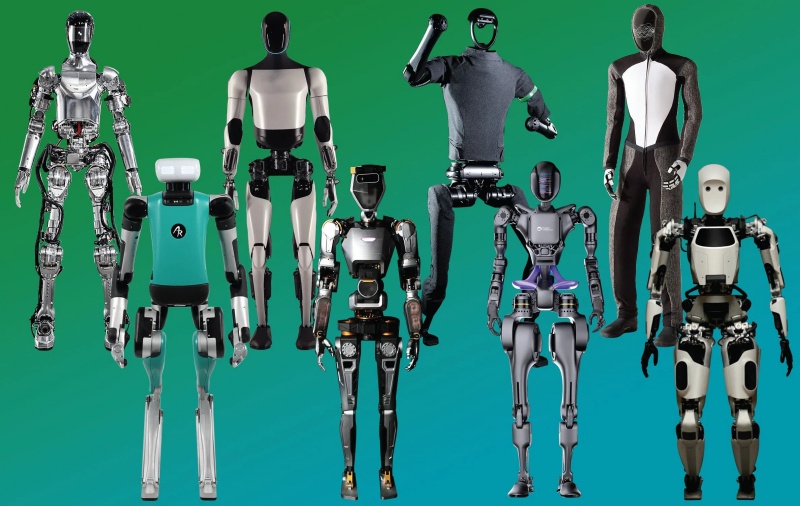
As humanoid robots progress toward mass production, efficient, precise, and cost-effective die-casting technology is set to play a pivotal role, replacing some machined parts and plastic components. Here’s how die casting enhances the manufacturing of these advanced robots:
1. Lightweighting Benefits for Robot Efficiency and Longevity
- Advanced Alloys: Die casting allows the use of alloys like magnesium and certain aluminum-based alloys, which are significantly lighter than machined aluminum yet retain comparable strength. For humanoid robots, this weight reduction is critical because it directly impacts their agility, balance, and power consumption.
- Improved Battery Life and Range: By reducing the robot's overall weight by 10-30%, die casting decreases the energy required to power motors and other moving parts. This weight reduction leads to extended battery life and longer operational periods between charges, essential for robots designed to perform continuous or high-energy tasks.
- Enhanced Mobility: Lighter components enable smoother and quicker movements, which is especially important for humanoid robots tasked with human-like interactions. The improved agility allows robots to navigate complex environments more easily and execute tasks with precision.
2. High Strength for Enhanced Structural Integrity
- Durability in Harsh Environments: Die-cast parts are known for their high tensile strength and fatigue resistance, which make them suitable for various robotic components, including the frame, limbs, and joint housings that bear significant loads.
- Extended Lifespan: Robots equipped with durable die-cast components are less prone to mechanical wear and stress fractures. This durability translates into a longer operational lifespan, reducing the need for frequent maintenance or replacements and offering a higher return on investment for industrial or consumer robots.
- Reduced Part Failure: Replacing machined aluminum parts with die-cast components minimizes the risk of failure in critical areas, such as joints and load-bearing connectors, ensuring that robots can withstand repetitive use and different types of workloads without compromising performance.
3. High Precision for Enhanced Functional Capabilities
- Exceptional Dimensional Accuracy: Die casting offers tight tolerances and excellent surface finishes, which are essential for robotic joints and movement systems. For example, die-cast aluminum can achieve tolerances up to ±0.005 inches, ensuring that moving parts operate smoothly without excess friction or play.
- Application in Key Components: Die casting is ideal for manufacturing small, precise parts like robotic fingers, gear housings, and sensor casings, where accuracy is paramount. These parts require consistency in size and shape to ensure the robot’s sensors, motors, and joints function accurately and reliably, crucial for applications like assembly, healthcare, and service robots.
- Improved Movement Precision: The high precision of die-cast components ensures that joints and connectors align perfectly, leading to smoother and more controlled movements. This is essential for humanoid robots that need to interact with delicate objects or operate in environments where exact movements are required.
4. Capability to Create Complex Shapes and Integrated Structures
- Consolidation of Parts: Die casting enables designers to combine multiple components into a single casting, reducing the number of individual parts and simplifying the robot’s assembly. For instance, a single die-cast unit might integrate both the motor housing and joint structure, reducing the complexity of assembly while improving robustness.
- Design Flexibility: Die casting can produce intricate, complex shapes that would be challenging or costly with traditional machining methods. This capability allows engineers to optimize the robot’s design for aesthetics and functionality without the limitations posed by other manufacturing techniques.
- Enhanced Reliability and Reduced Assembly Costs: By reducing the number of individual components, die casting decreases assembly time and labor costs. Fewer parts also mean fewer potential points of failure, enhancing the robot’s reliability over its lifetime.
5. Cost-Effectiveness for Scalability and Affordability
- High Production Efficiency: Die casting is a high-speed production process, which is ideal for manufacturing large volumes of parts quickly. With cycle times as short as 1 to 2 minutes per casting, this process enables high throughput, which is critical for mass-producing robots at an affordable price.
- Lower Per-Part Cost: The scalability of die casting significantly reduces the cost per part, making it feasible to produce high-quality components at a fraction of the cost compared to machined or 3D-printed parts. This reduction in production costs supports the affordability of humanoid robots, opening the door to consumer markets as well as commercial and industrial applications.
- Enhanced Material Efficiency: Die casting generates minimal waste, as excess material can often be recycled within the process. This efficiency not only reduces material costs but also supports sustainable manufacturing practices, which is increasingly important in today’s market.
Die Casting’s Role in the Future of Humanoid Robots
As we move toward an era of mass-produced humanoid robots, the need for affordable, durable, and high-precision components will only grow. Die-casting technology will likely play an even larger role, supporting advancements in robot mobility, interaction, and cost efficiency. By enabling lightweight, high-strength, and precise components at scale, die casting is poised to drive innovations that make humanoid robots accessible for various applications. Whether assisting in homes, healthcare facilities, factories, or service industries, these robots will transform how we interact with technology, boost productivity, and inspire new service models that redefine our work and personal lives.
In summary, die casting isn’t just a manufacturing method; it’s a cornerstone technology empowering the next generation of robotics, shaping a future where humanoid robots seamlessly integrate into everyday life.
Ningbo Fuerd was founded in 1987 and is a leading full-service die Casting Tooling, aluminum die casting, zinc die casting, and gravity casting manufacturer. We are a solution provider offering a wide array of capabilities and services that include engineering support, designing, molds, complex CNC machining, impregnation, tumbling, chrome, powder coating, polishing, assembly, and other finishing services. We will work with you as partners, not just suppliers.