Liquid Forging(Squeeze Casting)
FUERD focuses on the manufacturing of high-end aluminum alloy products, mainly using liquid forging technology. We have become a large-scale production base for high-strength, high toughness, and high-density aluminum alloy components in China. Our main product is automotive structural components. With core competitiveness in product development, process customization, extrusion molding, and precision machining, we further expand to the design process of vehicle manufacturers, providing customers with integrated solutions for the research and development, design, and production of automotive structural components.
Our liquid forging precision hardware, covering the research and development of professional equipment, mold manufacturing, and process research. We mainly produce aluminum alloy castings, alumina alloy castings, and high silicon hot forgings, which are widely used in various industries such as automotive parts, military, aerospace, and sports equipment. The company has accumulated years of experience in aluminum alloy forming and mold design and manufacturing, with a strong technical team and equipped with domestically advanced extrusion casting machines independently developed. In addition, we also have several senior engineers with extensive experience in mold design and production. as well as technicians with rich experience in die-casting, extrusion, and forging technology.
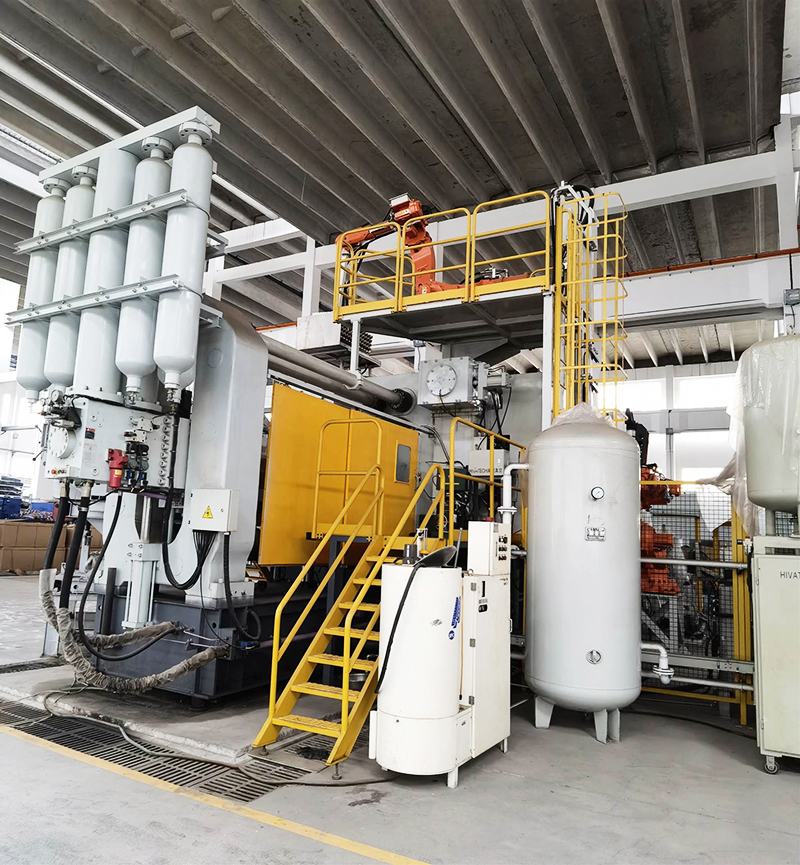
Liquid Forging Advantages
1. Our Liquid forging(squeeze casting)advantages
Firstly, squeeze casting technology effectively integrates the "performance and quality" of semi-solid die casting, while also combining the low cost of die casting with the high-performance advantages of forging. Our traditional casting (die casting) process has extremely high precision, producing products without pores or sand holes, with dense internal structure and no shrinkage porosity, and capable of T4/T6 heat treatment. In addition, our mechanical properties are comparable to forged products, and even surpass them in some aspects. For products with complex structures, our machining process reduces the amount of processing by 90% compared to forging, significantly reducing costs. Liquid forging, as a highly cost-effective process, is specifically designed to meet the complex structure and high performance requirements of products, fully combining the advantages of casting and forging.
2. Super aluminum alloy 6061-T6 material
The product manufactured using super aluminum alloy 6061-T6 material combined with liquid forging process can surpass the common hot forging process in the market in terms of tensile strength and yield strength. Its tensile strength can reach 350MPa, yield strength can reach 415MPa, and its performance can comprehensively surpass all casting processes. At present, squeeze casting and liquid forging are considered as ultra high end casting processes, especially in terms of product surface treatment, which can achieve anodizing and oxidation treatment of any color.
3. Equipment research and development/mold design/product production/integrated post-processingThe products produced by our squeeze casting equipment have reached the leading level in quality and performance in China. We provide one-stop services covering mold design, product production, and subsequent machining to ensure that our customers' needs are fully met.
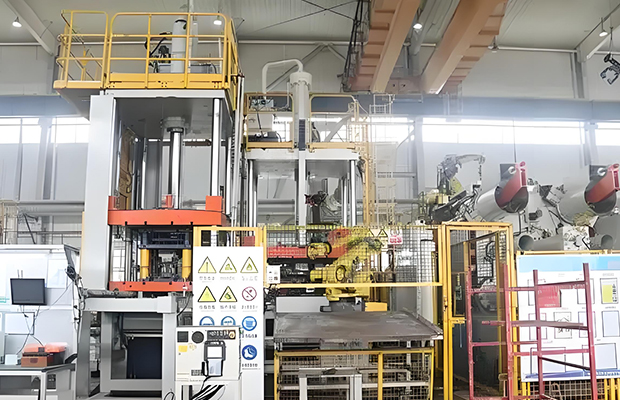
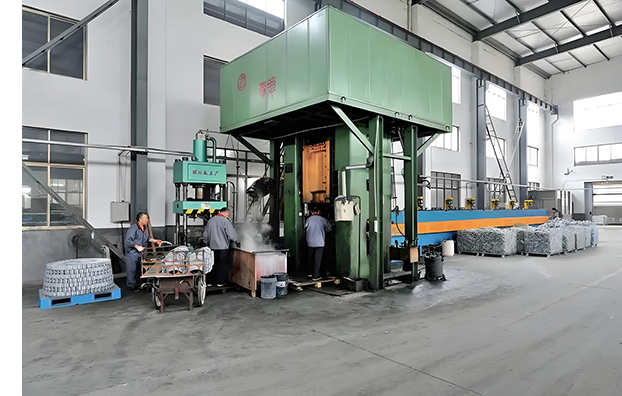
Equipment level
The liquid forging equipment owned by the company is in a leading position globally, using computer-controlled processes to achieve mechanized and automated production, demonstrating good process adaptability and ensuring the stability of product quality. This equipment is suitable for producing various cast aluminum alloys, partially deformed aluminum alloy parts, and thick walled castings with complex shapes. It is particularly suitable for extrusion casting of aluminum alloys, zinc alloys, and magnesium alloys that require high internal quality and mechanical properties. In addition, the company is equipped with three internationally advanced machining centers, including Demage five axis CNC machine tools, MAKINO F5 and MAKINO F8, and uses mold design and manufacturing software such as MAGMA, AnyCasting, NX UG, CATIA, and CAD Doctor to achieve seamless data integration from product design, virtual simulation to product manufacturing.
Ningbo Fuerd has a metal materials and automotive parts laboratory as its core, equipped with a series of inspection and testing equipment, including scanning electron microscopy, metallographic microscope, spectrometer, fluorescence analyzer, 200 ton tensile testing machine, X-ray machine, ultrasonic flaw detector, coordinate measuring instrument, and salt spray testing equipment. The company has established a full process inspection system from raw materials, semi-finished products to finished products to ensure the quality control of raw materials and the quality of products produced on site. At the same time, research, development, testing, and evaluation of supporting materials are carried out to meet the research and development needs of the company and customers for new products, and to enhance the comprehensive performance and quality of the products.
Technical Guarantee
Ningbo Fuerd regards liquid forging technology as one of its core technologies.
In the liquid forging process, filling and solidification are two key steps. Low speed filling and rapid high-pressure shrinkage solidification are key factors in ensuring dense microstructure of squeeze casting castings.
Filling: The filling process of the fully automatic liquid forging machine is driven by hydraulic pressure and has the characteristic of low-speed filling. The feeding port is located at the lower end and the exhaust port is located at the upper end. The filling speed can be infinitely adjusted, and the exhaust is smooth. There will be no bubbles generated during the filling process, and there are almost no porosity defects inside the casting.
Solidification: The solidification process of liquid forging requires the application of a relatively large mechanical pressure of about 100MPa (equivalent to 1000 atmospheres) to complete the shrinkage of the casting. Under this high pressure, when liquid metal solidifies, the structure is fine and dense, while avoiding defects such as porosity and shrinkage. The resulting castings have high comprehensive performance, approaching the level of forgings.
The production process technology of liquid forging and die casting ensures that aluminum alloy castings meet high standards in terms of dimensional accuracy, surface smoothness, and overall quality. The principle is to apply high mechanical pressure to the liquid or semi-solid metal or alloy entering the cavity of the liquid forging mold, to complete the forming and solidification process. Due to the simultaneous occurrence of high-pressure solidification and plastic deformation, the metal crystallizes and solidifies under pressure, and the shrinkage and porosity caused by solidification shrinkage are forcibly eliminated, resulting in liquid forging castings with dense structure, no porosity or porosity defects.