Aluminum die casting and CNC machining are two distinct manufacturing processes used to create components from aluminum materials. Each process has its own advantages, limitations, and applications. Here's a comparison of the two:
1. Aluminum Die Casting:
Process: Aluminum die casting involves injecting molten aluminum into a mold cavity under high pressure. Once the metal solidifies, the mold is opened, and the casting is removed.
Advantages:
- High production rates: Die casting is well-suited for high-volume production due to its rapid cycle times.
- Complex shapes: Die casting can produce intricate and complex shapes with thin walls and fine details.
- Surface finish: Die cast parts usually have a smooth surface finish that may require minimal post-processing.
Limitations:
- Material limitations: Die casting is typically limited to non-ferrous metals like aluminum, zinc, and magnesium.
- Tooling costs: Creating the molds (die tooling) can be expensive, especially for complex parts.
- Size constraints: Large components may be challenging to produce using die casting.
Applications: Aluminum die casting is commonly used for automotive parts, consumer electronics, housings, and other components requiring high production rates and complex shapes.
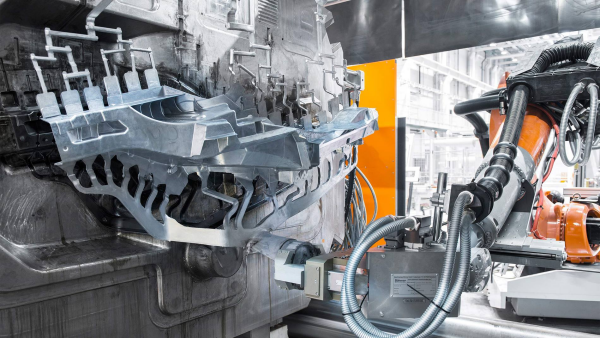
2. CNC Machining (Computer Numerical Control):
Process: CNC machining involves using computer-controlled machines to remove material from a solid aluminum block to achieve the desired shape and dimensions.
Advantages:
- Material variety: CNC machining can work with a wide range of materials, including aluminum and other metals, plastics, and even composites.
- Precision: CNC machining offers high precision and tight tolerances, suitable for critical components.
- Versatility: CNC machines can produce a variety of shapes and sizes, including complex geometries.
Limitations:
- Production speed: CNC machining is generally slower than die casting, making it less efficient for high-volume production.
- Labor and setup: Machining requires more manual labor and setup time, which can increase costs.
- Material waste: More material is usually wasted during machining compared to casting processes.
Applications: CNC machining is used for producing prototypes, low to medium production runs, and components requiring high precision, such as aerospace parts, medical devices, and custom components.
Key considerations for choosing between CNC machining or aluminum die casting
In some cases, a hybrid approach can also be used, where die casting is followed by CNC machining to achieve tight tolerances and intricate features on certain areas of the part. Collaborating with manufacturing experts and engineers can help you determine the most suitable process for your specific project.
Choosing between CNC machining and aluminum die casting requires careful consideration of several key factors. The decision should be based on your specific project requirements, including production volume, component complexity, material properties, lead time, and budget. Here are the key considerations for making an informed choice:
1. Production Volume:
- High Volume: Aluminum die casting is more suitable for high-volume production due to its rapid cycle times and efficiency in producing large quantities of parts.
- Low to Medium Volume: CNC machining is better for lower production volumes, prototypes, and smaller batches.
2. Component Complexity:
- Complex Shapes: If your component has intricate features, thin walls, or complex geometries, aluminum die casting may be more appropriate due to its ability to replicate these details accurately.
- Precision: For components requiring high precision and tight tolerances, CNC machining is a better choice.
3. Material Selection:
- Material Compatibility: Aluminum die casting is limited to non-ferrous metals like aluminum, zinc, and magnesium.
- Versatility: CNC machining can work with a wider range of materials, including metals, plastics, and composites.
4. Lead Time:
- Short Lead Time: CNC machining generally has shorter lead times, making it suitable for rapid prototyping and smaller production runs.
- Tooling Time: Aluminum die casting requires tooling (molds), which can add initial lead time.
5. Surface Finish:
- Smooth Finish: Aluminum die casting usually results in smoother surface finishes that may require minimal post-processing.
- Custom Finishes: CNC machining allows for more control over surface finishes, allowing you to achieve specific textures or patterns.
6. Cost Considerations:
- Tooling Costs: Aluminum die casting involves higher initial tooling costs due to mold creation.
- Material and Labor Costs: CNC machining may have higher material and labor costs, especially for larger volumes.
7. Design Changes:
- Design Flexibility: CNC machining is more adaptable to design changes during production, making it suitable for iterative prototyping.
- Tooling Changes: Once die casting tooling is created, design changes can be more challenging and costly to implement.
8. Environmental Impact:
- Material Waste: CNC machining generates more material waste compared to die casting, which could impact material costs and environmental considerations.
9. Post-Processing:
- Post-Processing Requirements: Consider any required post-processing steps, such as deburring, finishing, and assembly. CNC machining may require less post-processing.
10. Sustainability and Recyclability:
- Recyclability: Both processes use aluminum, a highly recyclable material. However, die casting may generate less waste due to the precision of the casting process.
Ultimately, the best choice depends on a holistic assessment of these factors in the context of your specific project goals, timeline, budget, and desired quality. Consulting with manufacturing experts, and engineers, and considering both short-term and long-term implications will help you make an informed decision that aligns with your project's requirements and constraints.
Choosing the right manufacturing process with a little help
Product teams should consider CNC machining if they require a medium to high production run of precise parts, a degree of design flexibility, and the capital to invest in CNC machines upfront or outsource production to a trusted partner. On the other hand, product teams should consider die casting if they want a cost-effective way to produce a very large number of identical parts and want to make the most of the money they spend on materials.
Manufacturing process comparisons like these are helpful for gaining clarity and viewing the key differences between two processes from a high level. Still, selecting the process that’s best suited to a project’s specific requirements can be challenging.