Classification and properties of die-casting aluminum alloys
Abstract: Aluminum alloy is currently the most widely used
die-casting material, widely used in the automotive industry, motorcycle industry, aerospace, and other industries. The characteristics of aluminum alloy are as follows: (1) The density of aluminum alloy is relatively small, only about 1/3 of that of iron, copper, and zinc, and its high specific strength and stiffness are its characteristics.
Classification of aluminum alloys:
Raw aluminum
1. Raw aluminum (flipped aluminum)
Raw aluminum is a low purity aluminum extracted from a naturally extracted chemical component, aluminum oxide. Raw aluminum is impure aluminum, which, like pig iron, can easily shatter with just a hard blow. The common aluminum products are light and thin, which is cooked aluminum. Aluminum alloy is smelted by adding a small amount of magnesium, manganese, copper and other metals into pure aluminum, greatly improving its corrosion resistance and hardness. Raw aluminum composition: less than 98% aluminum, brittle and hard, only sand casting products. Mature aluminum composition: More than 98% aluminum, soft in nature, capable of rolling or punching various utensils.
2. Die cast aluminum
Casting is a process of metal smelting and processing, usually using the
gravity of the metal to cast in the mold. But 'aluminum die-casting' is not done by gravity, but by applying a certain amount of pressure. It's a bit like 'injection molding'. But it has a set of high-tech core pulling, cooling and other systems. Overall, the material is delivered to the cavity to be cast through a centralized inlet, forming the parts. The aluminum suitable for die-casting process is die-casting aluminum, usually a die-casting aluminum alloy. 3. 6061 aluminum and 6063 aluminum are aluminum alloys represented by four digits, with magnesium and silicon as the main alloying elements and Mg2Si phase as the strengthening phase.
Types of die-casting aluminum alloys:
Al Mg alloy
The performance characteristics of Al Mg aluminum alloy are: good mechanical properties at room temperature; Strong corrosion resistance; The casting performance is relatively poor, with significant fluctuations in mechanical properties and wall thickness effects; During long-term use, there may be a decrease in the plasticity of the alloy due to aging, and even cracking of die castings; The tendency of stress corrosion cracking in die castings is also significant. The drawbacks of Al Mg alloy partially offset its advantages, limiting its application.
Al Zn alloy
After natural aging, Al Zn aluminum alloy die castings can achieve high mechanical properties. When the mass fraction of zinc is greater than 10%, the strength is significantly improved. The disadvantage of this alloy is poor corrosion resistance, tendency towards stress corrosion, and susceptibility to hot cracking during die casting. The commonly used Y401 alloy has good flowability and is easy to fill the mold cavity. The disadvantage is that it has a tendency to form pores, and is prone to hot cracking when the silicon and iron content is low.
Al Si alloy
Because Al Si aluminum alloy has the characteristics of small crystallization temperature interval, large solidification latent heat, large Specific heat capacity and small linear shrinkage coefficient of silicon phase in the alloy, its casting performance is generally better than other aluminum alloys, its filling capacity is also good, and the hot cracking and shrinkage porosity inclination are relatively small. Al Si Cocrystal contains the least brittle phase (silicon phase) with a mass fraction of only about 10%, so its plasticity is better than that of other Cocrystal aluminum alloys. The remaining brittle phase can be further improved by modification. The test also shows that Al Si Cocrystal still maintains good plasticity at the temperature near its solidification point, which is not found in other aluminum alloys. A considerable amount of Cocrystal is often required in the cast alloy structure to ensure its good casting performance; The increase of the number of Cocrystal will make the alloy brittle and reduce the mechanical properties. There is a certain contradiction between the two. However, due to the good plasticity of Al Si Cocrystal, which can better meet the requirements of both mechanical properties and casting properties, Al Si alloy is the most widely used die-casting aluminum alloy at present.
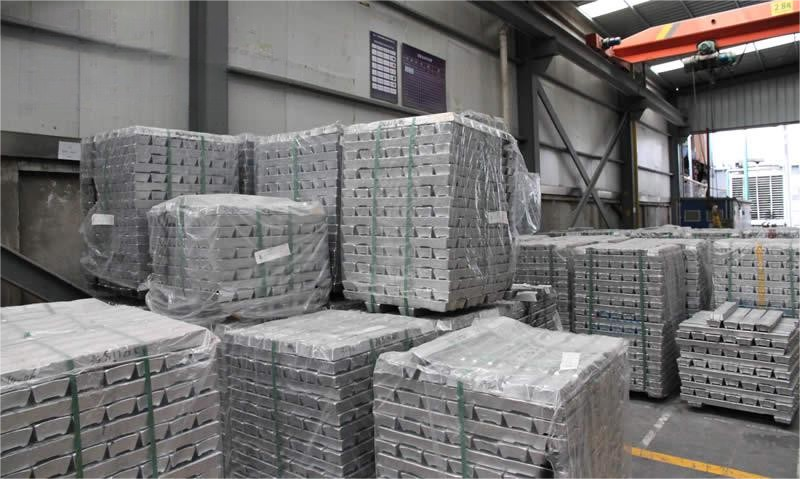
The aluminum alloy materials in aluminum alloy die castings are mainly divided into:
1. Aluminum silicon alloy: mainly including YL102 (ADC1, A413.0, etc.) and YL104 (ADC3, A360);
2. Aluminum silicon copper alloy: mainly including YL112 (A380, ADC10, etc.), YL113 (3830), YL117 (B390, ADC14) ADC12, etc;
3. Aluminum magnesium alloy: mainly including 302 (5180, ADC5,) ADC6, etc.
For aluminum silicon alloy and aluminum silicon copper alloy, as the name suggests, their composition is mainly composed of silicon and copper, except for aluminum; Usually, the silicon content is between 6 and 12%, which mainly plays a role in improving the fluidity of the alloy liquid; Copper content is only second, mainly playing a role in enhancing strength and tensile strength; The iron content is usually between 0.7 and 1.2%, and within this ratio, the demolding effect of the workpiece is the best; From its composition, it can be seen that this type of alloy is impossible to oxidize and color, and even with desilication oxidation, it is difficult to achieve the desired effect. For aluminum magnesium alloy, it can be oxidized and colored, which is an important characteristic that distinguishes it from other alloys. Currently, aluminum alloy die-casting parts generally use materials such as A380, A360, A390, ADC-1, ADC-12, etc. ADC12 is equivalent to A383 of the American ASTM standard, while A380 is equivalent to ADC10 of the Japanese standard. In Japan, ADC12 is widely used, but in the United States, A380 is widely used, and the composition of the two is relatively similar. However, the difference in Si content is relatively large, with ADC12 being 9.5-12% and A380i being 7.5-9.5%. In addition, there are also some differences in Cu content, with ADC12 being 1.5-3.5% and A380 being 2.0-4.0%. Other components are basically the same. The most commonly used materials in China are ADC12 and ADC6. The main difference between the two materials is that the content of Si, Fe, Cu, Zn, Ni, and Sn in ADC12 is higher than that in ADC6, while the content of Mg is lower than that in ADC6. ADC12 has better die-casting and mechanical processing properties, while its corrosion resistance is inferior to that of ADC6 material.
Types of die-casting aluminum alloys:
1. Al Mg alloy
The performance characteristics of Al Mg aluminum alloy are: good mechanical properties at room temperature; Strong corrosion resistance; The casting performance is relatively poor, with significant fluctuations in mechanical properties and wall thickness effects; During long-term use, there may be a decrease in the plasticity of the alloy due to aging, and even cracking of die castings; The tendency of stress corrosion cracking in die castings is also significant. The drawbacks of Al Mg alloy partially offset its advantages, limiting its application.
2. Al Zn alloy
After natural aging, Al Zn aluminum alloy die castings can achieve high mechanical properties. When the mass fraction of zinc is greater than 10%, the strength is significantly improved. The disadvantage of this alloy is poor corrosion resistance, tendency towards stress corrosion, and susceptibility to hot cracking during die casting. The commonly used Y401 alloy has good flowability and is easy to fill the mold cavity. The disadvantage is that it has a tendency to form pores, and is prone to hot cracking when the silicon and iron content is low.
3. Al Si alloy
Because Al Si aluminum alloy has the characteristics of small crystallization temperature interval, large solidification latent heat, large Specific heat capacity and small linear shrinkage coefficient of silicon phase in the alloy, its casting performance is generally better than other aluminum alloys, its filling capacity is also good, and the hot cracking and shrinkage porosity inclination are relatively small. Al Si Cocrystal contains the least brittle phase (silicon phase) with a mass fraction of only about 10%, so its plasticity is better than that of other Cocrystal aluminum alloys. The remaining brittle phase can be further improved by modification. The test also shows that Al Si Cocrystal still maintains good plasticity at the temperature near its solidification point, which is not found in other aluminum alloys. A considerable amount of Cocrystal is often required in the cast alloy structure to ensure its good casting performance; The increase of the number of Cocrystal will make the alloy brittle and reduce the mechanical properties. There is a certain contradiction between the two. However, due to the good plasticity of Al Si Cocrystal, which can better meet the requirements of both mechanical properties and casting properties, Al Si alloy is the most widely used die-casting aluminum alloy at present.
The forming process of die-casting aluminum is divided into:
2. Rough polishing to remove mold residues
Summary: When selecting die-casting materials, mechanical engineers should reasonably select the correct die-casting materials based on various factors such as product performance, process performance, production conditions, economy, and the characteristics of die-casting materials. Common die-casting materials for Machine element include aluminum alloy, zinc alloy and magnesium alloy.
Ningbo Fuerd was founded in 1987 and is a leading full-service die Casting Tooling, aluminum die casting, zinc die casting, and Gravity casting manufacturer. We are a solution provider offering a wide array of capabilities and services that include engineering support, designing, molds, complex CNC machining, impregnation, tumbling, chrome, powder coating, polishing, assembly, and other finishing services. We will work with you as partners, not just suppliers.