Comparing Cast Aluminum and Casting Iron: Which One is Better?
There is often confusion between cast aluminum and wrought iron, especially among those unfamiliar with the industry. In this article, we aim to clarify the differences between these two materials in terms of their physical and chemical properties.
What is Cast Aluminum?Cast aluminum is a metal that can be melted and poured into molds to create complex shapes. The metal can be poured at different pressures, affecting its quality. High-pressure casting results in less porosity and a more finished product, while low-pressure casting yields a less finished product with more porosity. Once the liquid metal settles and solidifies overnight, the mold is removed to reveal the newly formed aluminum replica.
Various casting methods, such as die casting, sand casting, centrifugal casting, and investment casting, can be used to shape cast aluminum. The choice of method depends on factors like the product's requirements, the industry's needs, the available resources, and the order quantity.
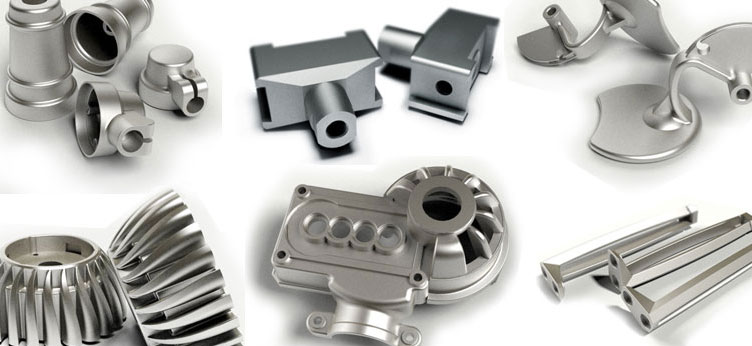
What is Casting Iron?
Casting iron, unlike cast aluminum, does not require a casting process. It is obtained by smelting iron, and once heated, it is ready to be worked with. Casting iron is known for its ductility and malleability. The more it is worked, the stronger it becomes, and its properties improve further.
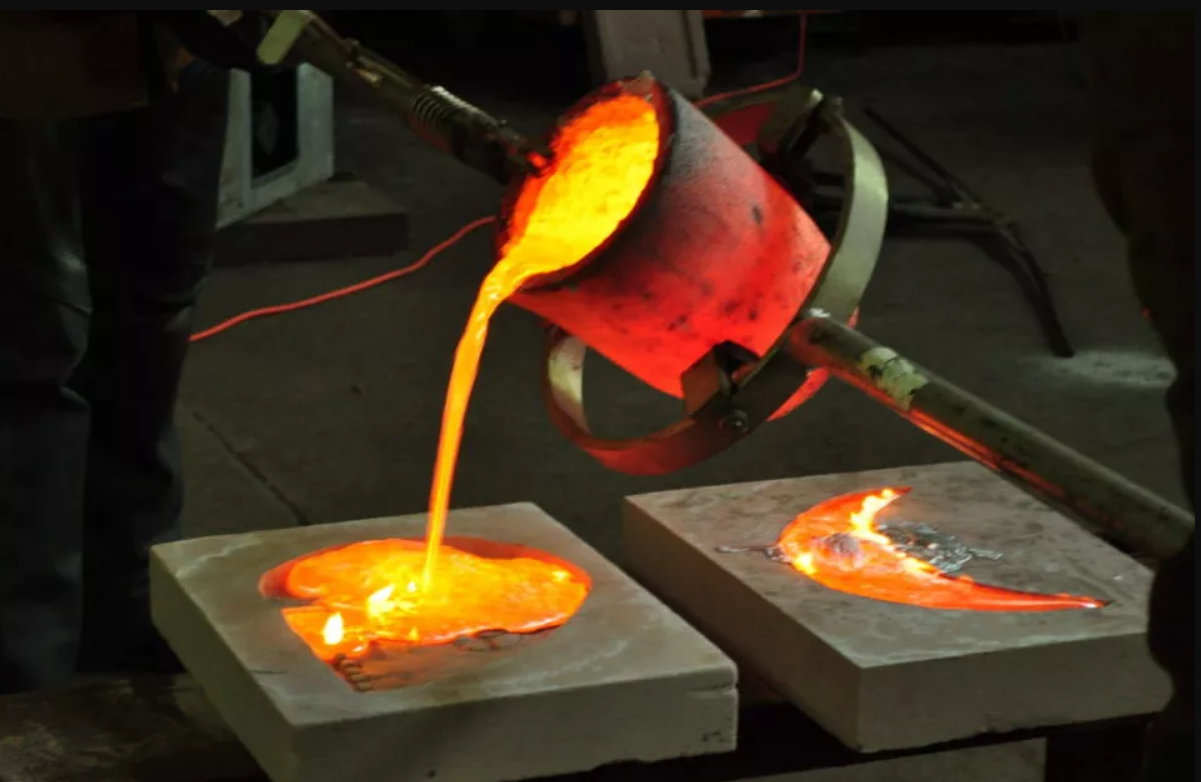
Why is Cast Aluminum Better than Casting Iron?When comparing cast aluminum and Casting iron, it is essential to consider the specific purpose and the crucial factors for your application.
Enhanced Ductility:
Cast aluminum can undergo processes to enhance its strength. It can be combined with other metals like magnesium-copper alloy and cerium, increasing its tensile strength and versatility. The additional heat applied to the metal makes it more ductile and malleable, allowing it to be shaped into complex tools.
Winner: Cast Aluminum
Corrosion Resistance and Precautions:
Wrought iron is highly susceptible to corrosion when exposed to moisture. It requires external protection such as powder coating or color coating to prevent rusting. In contrast, cast aluminum naturally forms a protective oxide layer, reducing its vulnerability to corrosion.
Winner: Cast Aluminum
Cost:
Cast aluminum is more affordable than wrought iron due to easier production processes and lower labor requirements. Moreover, wrought iron's maintenance costs are higher due to its tendency to corrode, while cast aluminum is corrosion-resistant.
Winner: Cast Aluminum
Weight:
Wrought iron is significantly heavier than cast aluminum. This characteristic makes cast aluminum popular for automotive parts as it provides lightweight options, allowing for easy handling and transportation.
Winner: Cast Aluminum
Strength and Durability:
Casting iron excels in terms of strength and durability. While cast aluminum is also durable and strong, wrought iron generally offers superior durability.
In conclusion, both cast aluminum and Casting iron have their advantages and uses. Cast aluminum is preferred for its enhanced ductility, corrosion resistance, affordability, lighter weight, and suitability for various applications. On the other hand, wrought iron stands out with its strength and durability. The choice between the two ultimately depends on the specific requirements and priorities of the intended use.
Ningbo Fuerd was founded in 1987 and is a leading full-service die Casting Tooling, aluminum die casting, zinc die casting, and Gravity casting manufacturer. We are a solution provider offering a wide array of capabilities and services that include engineering support, designing, molds, complex CNC machining, impregnation, tumbling, chrome, powder coating, polishing, assembly, and other finishing services. We will work with you as partners, not just suppliers.