Enhanced Precision in Die Casting Through Advanced Mold Temperature Control
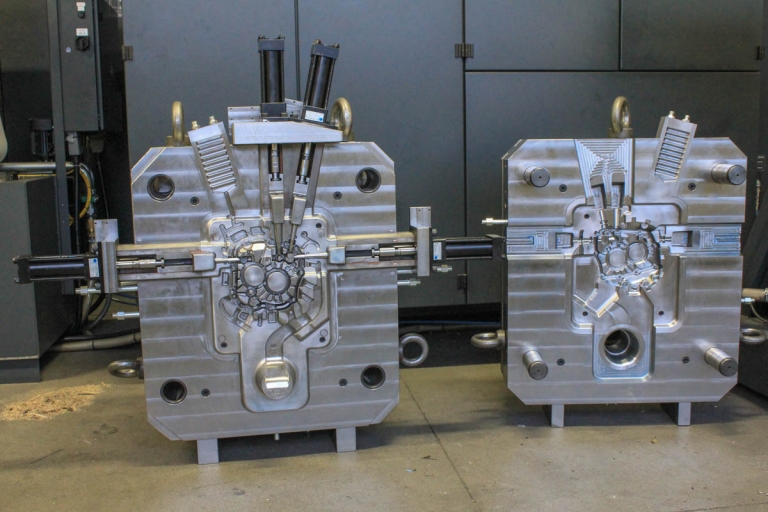
In die casting, where products are pivotal in industries like automotive manufacturing, the quest for heightened production efficiency, superior product quality, prolonged mold lifespan, and cost-effectiveness has surged. This escalating demand underscores the imperative for precise mold temperature regulation alongside increased process automation and intelligence.
Achieving Optimal Thermal Balance: The thermal equilibrium of molds profoundly influences casting quality, mold longevity, and overall production efficiency in die-casting processes. Conventional manual control methods for temperature regulation, while relying on human expertise, often lack repeatability and prove inefficient. Moreover, manual interventions hinder the timely detection of parameter changes or emerging faults, leading to frequent product scrap and substantial losses.
Traditional mold cooling methods primarily rely on cooling water channels and localized cooling points. However, manually managing cooling water flow, pressure adjustments, and monitoring conditions based on experience often result in unstable mold temperatures, impacting both product yield and production efficiency. Moreover, imbalanced mold temperatures can cause issues such as aluminum sticking, necessitating frequent mold shutdowns for polishing and negatively impacting efficiency and product quality. Conversely, inadequate mold temperatures can lead to molten aluminum flow problems, resulting in defects like cold shuts.
Additionally, continuous cooling water usage leads to a post-mold opening temperature drop, coupled with high mold surface stress, potentially causing surface cracking. To address these challenges, a novel mold temperature control system, the "Temperature Control Island," has emerged.
Components of the Temperature Control Island: This innovative system comprises a pure water machine, a chiller, an intermediate water tank, a fine core point cooler, and a high-pressure mold cooler. Employing pure water ensures water quality, while an independent closed circulation system prevents cooling pipeline blockages due to water quality issues. The system utilizes both atmospheric and high-pressure cooling methods, each with intermittent cooling functions, allowing precise temperature control.
Operational Workflow: During automated die-casting production, the Temperature Control Island receives signals such as "injection start" or "mold locked" from the die-casting machine. It then regulates cooling water flow based on preset process requirements, with each cooling circuit individually controllable for on/off settings, timing, delay, and flow rate. Following the cooling process, automated compressed air purging clears residual cooling water, preventing potential porosity issues.
Advantages of Temperature Control Islands: The closed, independent cooling system using pure water effectively prevents cooling pipeline blockages, while tailored control for different zones optimizes temperature regulation, reducing defects. Intermittent cooling minimizes temperature drops post-mold opening, extending mold lifespan. Furthermore, efficient parameter storage facilitates rapid production transitions during mold changes, reducing downtime and enhancing efficiency.
Conclusion: Traditional cooling methods often struggle with efficient, partitioned control in complex molds. Temperature Control Islands offer precise temperature regulation tailored to product and mold structure, improving quality, efficiency, and resource utilization in die-casting processes. As the die-casting industry advances, solutions like the Temperature Control Island exemplify its commitment to automation, intelligence, and high-quality production.