How to Design a Die Casting Mold?
Designing a die casting mold is a critical aspect of the manufacturing process, ensuring the production of high-quality metal parts with precision and efficiency. Here's a step-by-step guide on how to design a die casting mold:
-
Define Requirements and Objectives:
- Understand the specifications of the final part, including dimensions, tolerances, material requirements, and surface finish.
- Identify the production volume and cycle time requirements.
- Determine any specific design constraints or considerations, such as draft angles, undercuts, and parting lines.
-
Conceptualize the Design:
- Collaborate with engineers and designers to conceptualize the mold design based on the part's geometry and requirements.
- Utilize CAD (Computer-Aided Design) software to create detailed 3D models of the mold components, including the mold cavity, core, slides, ejector system, and cooling channels.
- Consider factors such as parting lines, gating system, venting, and ejection mechanisms during the design phase.
-
Material Selection:
- Choose materials for the mold components based on factors such as thermal conductivity, wear resistance, and machinability.
- Common materials for die casting molds include tool steel, such as H13, and high-strength aluminum alloys for certain components.
-
Design for Manufacturability:
- Ensure that the mold design is optimized for manufacturability, considering factors such as tooling costs, machining capabilities, and ease of assembly.
- Design the mold with appropriate draft angles and fillets to facilitate part ejection and reduce the risk of defects.
- Incorporate features such as cooling channels to control the temperature of the mold during casting and minimize cycle times.
-
Gating and Runner System:
- Design the gating and runner system to facilitate the flow of molten metal into the mold cavity with minimal turbulence.
- Select gate locations and sizes to ensure proper filling of the cavity and minimize the risk of defects such as air entrapment and porosity.
-
Venting and Overflow Design:
- Include venting channels or vents in the mold design to allow the escape of air and gases during casting.
- Design overflow or overflow wells to capture excess molten metal and prevent defects such as flash and short shots.
-
Simulation and Analysis:
- Conduct mold flow analysis using specialized software to simulate the filling and solidification of molten metal in the mold cavity.
- Analyze the simulation results to optimize the mold design, identify potential issues, and make necessary adjustments.
-
Prototyping and Testing:
- Fabricate prototype molds or prototype parts using rapid prototyping techniques such as 3D printing.
- Test the prototypes to evaluate mold functionality, part quality, and performance under simulated production conditions.
-
Refinement and Finalization:
- Iterate on the design based on feedback from prototype testing and simulation analysis.
- Fine-tune the mold design to address any issues and optimize performance.
- Finalize the design for production, ensuring that all specifications and requirements are met.
-
Documentation and Release:
- Prepare detailed documentation, including engineering drawings, bill of materials, and manufacturing instructions.
- Release the finalized mold design for production, following established quality assurance processes and procedures.
By following these steps, you can effectively design a die casting mold that meets the requirements of your project and ensures the production of high-quality metal parts.
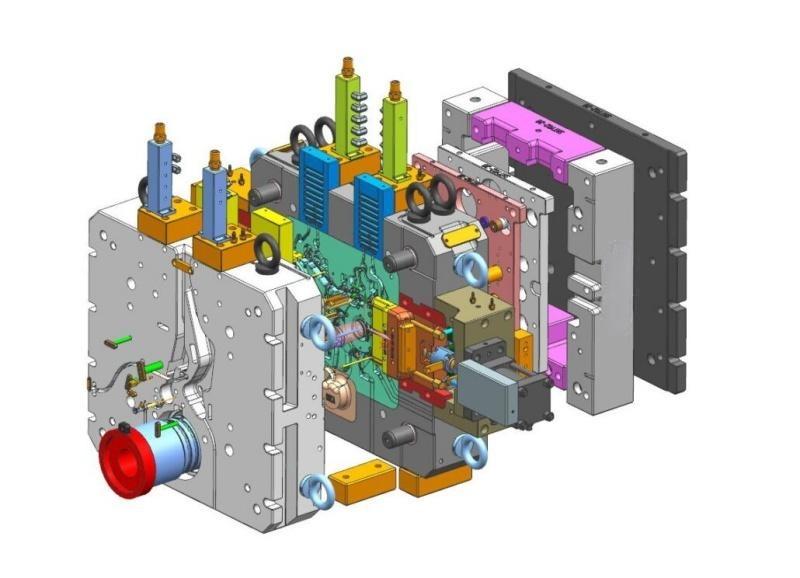
Ningbo Fuerd was founded in 1987 and is a leading full-service die Casting Tooling, aluminum die casting, zinc die casting, and gravity casting manufacturer. We are a solution provider offering a wide array of capabilities and services that include engineering support, designing, molds, complex CNC machining, impregnation, tumbling, chrome, powder coating, polishing, assembly, and other finishing services. We will work with you as partners, not just suppliers.