Sheet Metal Fabrication: Understanding Costs and Cost-Saving Tips
Sheet metal fabrication stands out as a highly popular process in prototyping, offering a versatile approach to creating durable parts, ranging from prototypes to high-volume production components. Despite its numerous commercial benefits, the cost associated with sheet metal fabrication remains a key consideration for product developers.
Every aspect of a sheet metal fabrication project incurs a specific cost, encompassing design, potential prototyping, finishing processes, and more. Material costs are also integral, making it imperative to develop a cost-saving strategy to optimize the outcome of your sheet metal project.
Estimating Sheet Metal Fabrication Costs: A Step-by-Step Guide
In order to estimate the costs associated with sheet metal fabrication, it's crucial to follow a systematic approach. The following steps outline a cost estimation process:
-
Break Down the Production Cycle:
- Divide the production cycle into simpler processes, focusing on one cycle at a time.
-
Calculate the Cost of Raw Materials:
- Estimate the quantity of materials required for a single product.
- Utilize a sheet metal fabrication cost calculator for raw material cost estimation.
-
Add the Cost of Machining:
- Determine the hourly cost of the machine, its efficiency, and cycle time.
- Calculate machining cost using the provided formula.
-
Repeat the Calculation for Different Production Phases:
- Apply the same process for each phase or machine involved in the production cycle.
-
Total Product Cost:
- Sum up the raw material cost and machining cost to obtain the total production cost for one piece.
Factors Affecting Sheet Metal Fabrication Costs: An Overview
Several factors influence the costs associated with metal fabrication projects:
-
Installation Pricing:
- Ease of installation and duration impact costs.
- Installation expenses may include skilled professionals, permits, safety gear, and transportation.
-
Cost of Raw Materials:
- Material selection and market fluctuations affect overall prices.
- Thickness of the metal contributes to material and labor costs.
-
Plating and Welding Costs:
- Welding pre-plated sheet metal can be unsafe and costly.
- Considerations for plating after fabrication may increase costs and lead times.
-
Physical Work Required:
- Skilled fabricators and specialized equipment affect labor costs.
- Computer-aided designs and CAD/CAM software contribute to expenses.
-
Metal Structure and Design Complexity:
- Complex designs with multiple bends, cuts, and welds increase costs.
- Tighter tolerances and intricate designs require more time and labor.
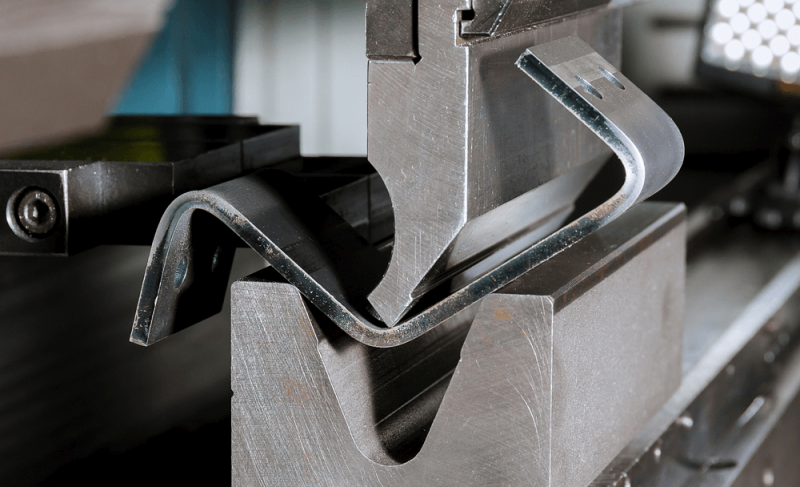
Tips for Reducing Sheet Metal Fabrication Costs: Practical Strategies
To minimize costs in sheet metal fabrication, consider the following tips:
-
Choose the Right Raw Materials:
- Opt for stock sizes and affordable materials for prototypes.
- Collaborate with fabricators buying mill-direct for lower bulk pricing.
-
Use a Common Gauge of Sheet Metal:
- Design with standard sheet gauges and sizes to reduce costs.
- Standardize gauges to avoid specially ordered materials.
-
Avoid Complicated Design Elements:
- Simplicity in design minimizes costs associated with cuts, bends, and welds.
- Opt for simpler angles and features to enhance cost-effectiveness.
-
Consider Finishing Options Wisely:
- Choose finishes based on application needs and aesthetic requirements.
- Delay finishes like engraving until the final stages of product development.
-
Contact a Professional Fabricator:
- Choose a full-service fabricator with in-house capabilities.
- Collaboration with professionals streamlines the process, reducing costs.
-
Other Considerations:
- Stick with appropriate tolerances to avoid additional costs.
- Utilize optimal bend radius for efficient manufacturing.
- Consider fast and readily available fasteners to minimize expenses.
Conclusion: Cost-Effective Sheet Metal Fabrication
Sheet metal fabrication costs are a critical aspect of project planning. By employing the outlined cost estimation process and implementing strategic tips for cost reduction, developers can achieve high-quality sheet metal parts at competitive prices. Partnering with professional fabricators with in-house capabilities further ensures efficiency and cost-effectiveness in the fabrication process.
Ningbo Fuerd was founded in 1987 and is a leading full-service die Casting Tooling, aluminum die casting, zinc die casting, and gravity casting manufacturer. We are a solution provider offering a wide array of capabilities and services that include engineering support, designing, molds, complex CNC machining, impregnation, tumbling, chrome, powder coating, polishing, assembly, and other finishing services. We will work with you as partners, not just suppliers.