In order to fill all the concave holes and depths of die casting die better and ensure the metal flow, the casting temperature of metal should be selected correctly when using die casting die. The pouring temperature of alloy die casting liquid is as follows:
Material name Die casting liquid temperature / ℃
Aluminum alloy 620-690
Magnesium alloy 700-740
Copper zinc alloy 850-960
Selection principle of die casting alloy temperature:
1) The lower the temperature of the metal poured in, the longer the life of the die casting die;
2) Only by using low temperature die casting can the increase of the depth of exhaust tank be reduced and the risk of metal splashing can be reduced;
3) The low temperature die casting can reduce the chance of the chamber and the top bar to be locked;
4) The shrinkage hole and crack in the casting can be reduced by low temperature die casting.
In a word, the temperature of die casting alloy is better than that of low temperature die casting when the process conditions permit.
After the die casting is finished, the die-casting can be stabilized and qualified castings can be produced by adjusting the trial die and selecting the correct die casting conditions and process parameters.
Before the die test, the mold testing personnel shall check the alloy raw materials for die casting in advance to understand the characteristics and die-casting characteristics of alloy materials; The structure of the die, the performance of the die casting machine, the die casting conditions, the die casting technology and the operation method should be understood.
The key to the adjustment of die test is to select the die casting forming conditions correctly. It is often encountered that even if the design and manufacture of die are very correct, due to the improper selection of die casting conditions, the qualified castings can not be pressed. On the contrary, in some cases, the defects of die can be overcome by adjusting the conditions of die casting forming, and the qualified casting can be pressed out. Therefore, the die testing personnel must be familiar with the role and relationship of various die casting forming conditions, the operation principle of the die, etc. in order to correctly select and adjust the die casting forming conditions.
The contents of die casting forming conditions are: melting temperature of material, die temperature and molten liquid temperature during pressing; The injection pressure, the lock force, the opening force of die casting machine, the injection ratio and the injection speed required according to the conditions of the parts are determined. Finally, the die casting parts can be completed only after the condition of die casting products is trimmed.
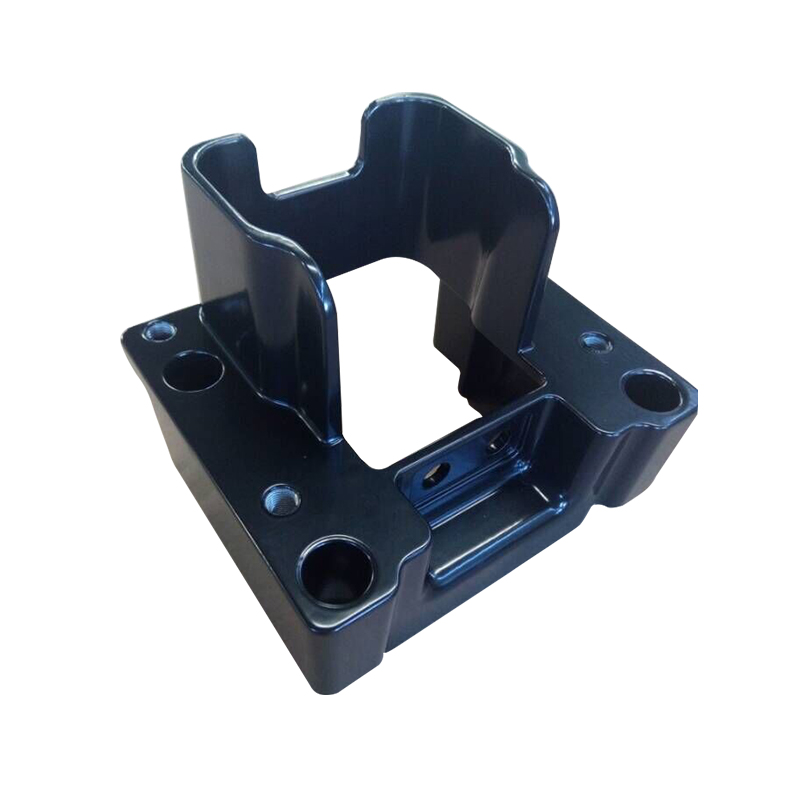