What is the Difference Between Zinc Die Casting Parts and Aluminum Die Casting Parts?
Both
zinc die casting parts and
aluminum die casting parts are widely used for industrial purposes. So what are the differences between the two types of die castings? The main difference lies in the characteristics and characteristics and applications of zinc alloy die casting and aluminum alloy.
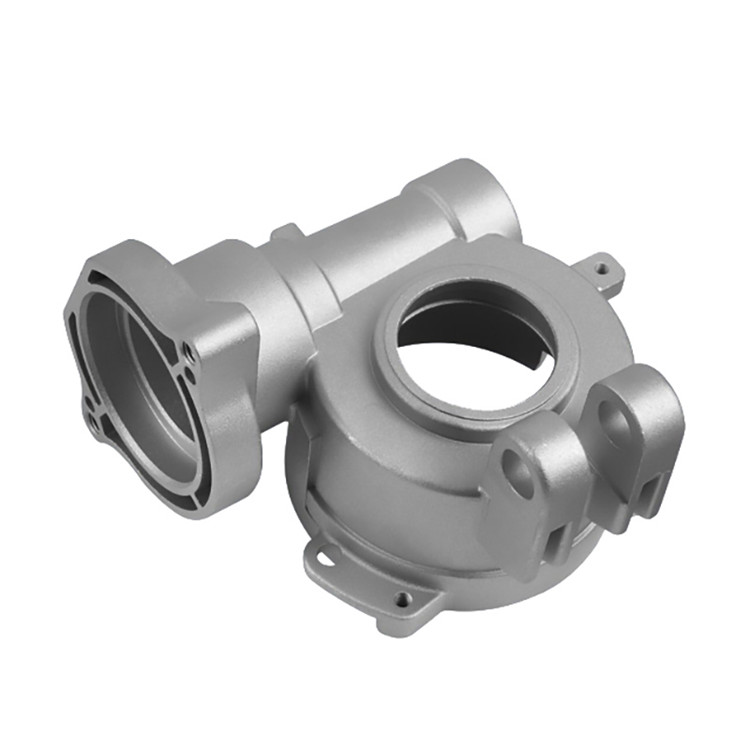
1. Suitable for mass production
2. Production cost reduction
3. Good surface quality, which can reduce the cost of surface treatment
4. The cost of mold opening is lower than that of aluminum alloy
5. Excellent fluidity and high mechanical strength
6. The product has high dimensional accuracy
7. The thin wall of the product can be at least 0.5mm
8. Zinc alloy die-casting mold has a long service life
There are many zinc alloy die-casting products. Usually, the fields where zinc alloy die-casting is more commonly used include: 3C products, hardware, automobile and motorcycle parts, bicycle parts, etc.
1. Lighter texture, one third of steel
2. High strength, the use of various alloy additions, rolling, forging and heat treatment processes of different grades can produce various aluminum alloy products with a strength of HB25o-HB167o
3. Corrosion resistance
4. High electrical conductivity and thermal conductivity
5. More environmentally friendly
6. Low temperature resistance, in the state of ultra-low temperature, aluminum does not have the embrittlement problem of ordinary carbon steel.
The areas where aluminum alloys are often used include: electrical appliances, electronic cooling systems, home hardware, food utensils (aluminum cans, flexible packaging), containers, transportation tools, etc.
Zinc alloys have the highest hardness and strength among various (low aluminum) zinc alloys. Its high copper content ( 3% ) causes some changes in the properties of the alloy as it ages, these changes include an increase in size(Increase 0.0014 mm per mm after 20 years), reduce drag and impact strength. Compared with 3# and 5# zinc alloys, 2# zinc alloys have better creep resistance (shape under stress at high temperature) and wear resistance.It can maintain high strength and hardness during aging. 2# zinc alloy is also used in gravity casting, such as making metal molds or injection tools.
Zinc alloy has always been the material of choice for the die casting industry, which best balances the requirements of physical and mechanical properties. Its excellent castability and long-lasting dimensional stability make more than 70% of the die-casting products made of zinc alloys use 3# zinc alloy. 3# zinc alloy is also particularly suitable for surface treatment such as electroplating, painting and chroming.
The copper content of zinc alloy is between 3# and 5#, 4# zinc alloy is more effective than 3# to reduce the sticking phenomenon of some castings, while 4# zinc alloy still maintains the same softness as 3# zinc alloy.Compared with 3# zinc alloy, the hardness and strength of zinc alloy are higher, but the flexibility is lower, which may be affected when the casting needs deformation processes such as bending and rolling. The characteristic change of 5# zinc alloy is due to the addition of 1% copper, which is different than that of alloy casting, and its resistance to creep (deformation when heated at high temperature) is better than that of 3# zinc alloy. It is also suitable for electroplating, machining and general surface treatment.
Zinc alloys were developed for gravity casting, but are now commonly used in high pressure casting. It has higher hardness, strength and creep resistance (deformation under high temperature stress) than 3# zinc alloy and 5# zinc alloy. 8# is also suitable electroplating and other surface treatments are the same as those of 5# zinc alloy. Therefore, when the performance of 3# and 5# fails to meet the requirements, the high strength and creep resistance of 8# is another option.
Ningbo Fuerd was founded in 1987, is leading full-service die Casting Tooling, aluminum die casting, zinc die casting, Gravity casting manufacturer. We are a solution provider offering a wide array of capabilities and services that include engineering support, designing, molds, complex CNC machining, impregnation, tumbling, chrome, powder coating, polishing, assembly and other finishing services. We will work with you as partners not just suppliers.