-
Material Properties:
- Zinc:
- High strength and hardness: Zinc alloys offer excellent strength and hardness, making them suitable for applications requiring robustness.
- Superior dimensional stability: Zinc alloys exhibit minimal shrinkage during solidification, resulting in accurate and dimensionally stable castings.
- Good corrosion resistance: Zinc alloys provide inherent corrosion resistance, requiring minimal surface treatment.
- High ductility: Zinc alloys can undergo significant deformation without fracturing, making them suitable for forming complex shapes.
- Aluminum:
- Lightweight: Aluminum alloys are significantly lighter than zinc, making them ideal for applications where weight reduction is critical.
- Good strength-to-weight ratio: Aluminum alloys offer a favorable strength-to-weight ratio, providing adequate strength while minimizing weight.
- High thermal conductivity: Aluminum alloys dissipate heat efficiently, making them suitable for heat dissipation applications.
- Excellent machinability: Aluminum alloys are relatively easy to machine, facilitating post-casting operations.
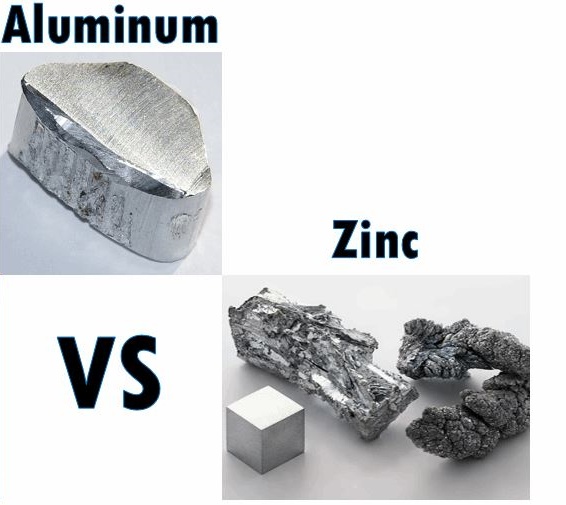
-
Cost:
- Zinc: Generally, zinc alloys are more economical than aluminum alloys for die casting. They have lower melting temperatures and faster solidification rates, resulting in reduced energy consumption and cycle times.
- Aluminum: Aluminum alloys may be more expensive than zinc alloys due to higher material costs and longer processing times.
-
Production Requirements:
- Zinc: Zinc die casting typically requires lower operating temperatures and shorter cycle times compared to aluminum die casting, resulting in faster production rates and lower energy costs.
- Aluminum: Aluminum die casting may require higher operating temperatures and longer cycle times, potentially leading to higher energy consumption and production costs.
-
Surface Finish:
- Zinc: Zinc alloys generally provide a smoother surface finish than aluminum alloys, requiring minimal post-casting surface treatment.
- Aluminum: Aluminum alloys may require additional surface treatments such as machining, polishing, or coating to achieve the desired surface finish.
-
Specific Application Needs:
- Zinc: Zinc alloys are commonly used in applications requiring intricate designs, tight tolerances, and excellent surface finish, such as automotive components, electrical connectors, and hardware fittings.
- Aluminum: Aluminum alloys are preferred for applications requiring lightweight, high strength, and good thermal conductivity, such as automotive parts, electronic housings, and aerospace components.
In summary, the choice between zinc and aluminum for a die-casted product depends on factors such as material properties, cost considerations, production requirements, surface finish requirements, and specific application needs. Both materials offer unique advantages and are suitable for a wide range of applications in various industries.