New energy motor controller Five-in-one controller for pure electric buses
New energy vehicles differ from traditional vehicles in that they use batteries as the power to drive the vehicle. Due to the limitations of the weight and range of power batteries, as well as the high pressure of energy-saving and emission-reduction policies in automobiles, the lightweight of its body has become a top priority for car manufacturers in vehicle design and material applications. Therefore, battery-powered new energy vehicles require more weight reduction than traditional cars. This has also opened up a broader market space for lightweight materials such as aluminum.
In the lightweight materials of automobiles, aluminum alloy materials have a higher comprehensive cost-effectiveness than steel, magnesium, plastic, and composite materials, and have significant advantages in terms of application technology, operational safety, and recycling. The density of aluminum is only 1/3 that of steel, and its weight reduction and energy-saving effects are significant. It can also better improve ride comfort while ensuring safety. At the same time, aluminum is easier to recycle and reuse. The comprehensive cost-effectiveness advantage of aluminum determines that it is the best choice for lightweight automotive applications.
The application of aluminum in new energy vehicle components mainly includes the body, wheel hub, chassis, collision beam, power battery, etc. According to the classification of processing forms, automotive aluminum is mainly divided into three forms: die-casting, extrusion, and rolling. Among them, the usage of die-casting parts accounts for about 80%, and extrusion and rolling parts account for about 10% each. Die-casting parts are mainly used for engines, wheels, and other parts. Extrusion parts are mainly used for seats, luggage racks, door beams, etc., and rolling parts are mainly used for producing aluminum plates for car bodies and other parts.
The vehicle body includes a body skeleton made of high-performance aluminum profiles, skin, and doors made of high-precision aluminum plates, aluminum alloy wheels (cast aluminum wheels or forged aluminum wheels), and the chassis includes high-strength cross-section aluminum profile structural components and aluminum alloy forgings. In the past, new energy vehicles often used steel materials to make power battery trays for electric vehicles. However, the application of aluminum alloy materials has gradually surpassed that of steel, and aluminum alloys have obvious advantages in density, compression, and welding.
IATF16949&ISO 9001 CERTIFIED
FUERD was founded in 1987 with a small die casting tooling and die casting facility located in Ningbo. Today, the company has become one of the largest and most diversified die casting companies in China. FUERD grew considerably and built an expert in large, thin-walled die castings serving the lighting and auto industries.
✧ Products Description:
Mold Material |
SKD61, H13 |
Cavity |
Single or multiple mold |
Mold Life Time |
50K times product |
Product Material |
1) ADC10, ADC12, A360, A380, A413, A356, LM20, LM24 2) Zinc alloy 3#, 5#, 8# |
Surface Treatment |
1) Polish, powder coating, lacquer coating, e-coating, sand blast, shot blast, anodyne 2) Polish + zinc plating/chrome plating/pearl chrome plating/nickel plating/copper plating |
Size |
1) According to customers' drawings 2) According to customers' samples |
Drawing Format |
step, dwg, igs, pdf |
Certificates |
ISO 9001:2015 & IATF 16949 |
Payment Term |
T/T, L/C, Trade Assurance |
✧ Packaging Details:
1. Plastic bag with pearl-cotton package.
2. To be packed in cartons.
3. Use glue tape to seal cartons.
4. Deliver out by sea or air.
Or according to customers' requirements.
Each carton is less than 15kg.
✧ Lead Time:
Quantity(Pieces) |
1 - 3000 |
>3000 |
Est. Time(days) |
25 |
To be negotiated |
✧ Equipment:
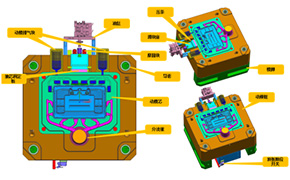 |
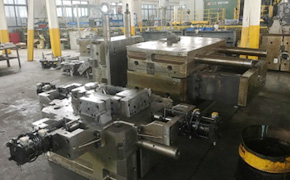 |
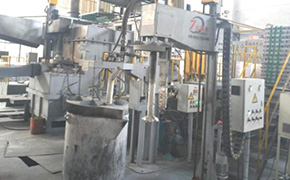 |
Product DFM
|
Mold Making
|
Centralized smelting
|
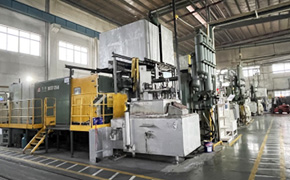 |
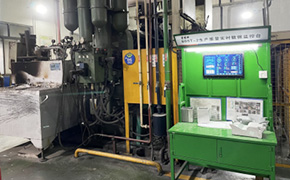 |
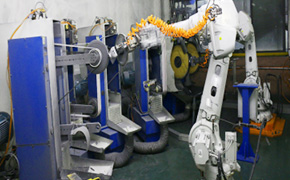 |
Die casting
|
Casting monitoring
|
Automatic polishing
|
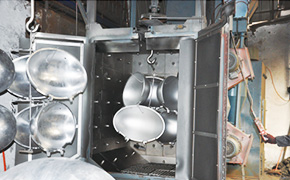 |
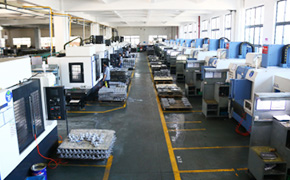 |
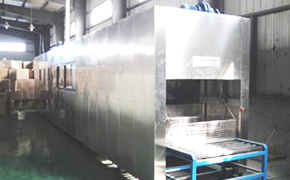 |
Shot blasting
|
CNC Machining
|
Ultrasonic cleaning
|
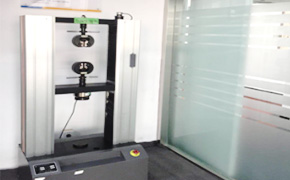 |
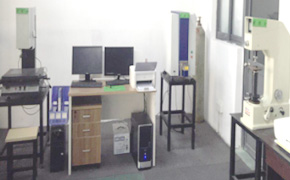 |
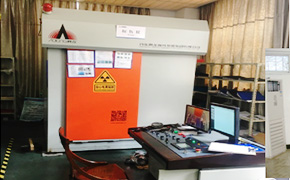 |
Tensile testing
|
Spectrum analyzer
|
X-Ray:Check the shrinkage sand hole inside the produc
|
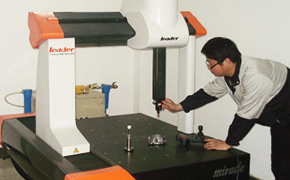 |
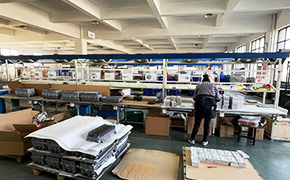 |
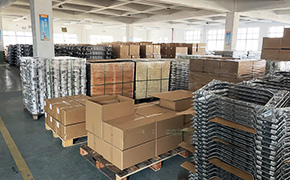 |
CMM:Check the product position, parallelism, isometric tolerance and dimension
|
Final inspection line
|
Standard Or Custom Packing
|
✧ Why choose us:
-
1. Engineering Designing
Innovative tooling designs engineered and optimize your new and existing parts...at FREE COST to You!
-
2. Lower Tooling Costs
Quickly soft tooling to make under 1000 parts for your testing to avoid die casting mold investment risk and save product test time!
-
3. Lower Part Costs
Automatic and manual die casting production process to save part costs.
-
4. Assembly line
Final assembly line to ensure all parts fit together for the whole project requirement.
-
5. Customer Service
Professional project engineers directly work with your design engineers from the designing stage through product delivery.
-
6. Reliable Quality
Integrated Quality Management system IATF16949 & ISO 9001 certified from RFQ to delivery to control of good quality.
-
7. On-time Delivery
Above 98% of molds and products can be shipped on time.
-
8. Manufacturer experience
More than 35 years of manufacturer experience with satisfied customers.
✧ FAQ:
-
1. Are you a manufacturer or a trading company?
Our factory provides mold, die casting, CNC, and all related processes.
-
2. How to quote?
Received the sample or drawing in CAM/STP/IGS form, then we will make the quotation.
-
3. What kind of production service do you provide?
Mold making, die casting, CNC machining, stamping, plastic injection, assembly, and surface treatment.
-
4. What's the production time for new molds and mass production?
30-60 days to make the molds, mass production takes around 30-45 days, also we can speed up the process urgently needed need.
-
5. Payment terms
Tooling cost: TT 50% with order, the balance the after sample is approved.
Mass production: TT 50% with order, the balance at sight of B/L
-
6. How about the packing?
Both standard and customized will be available.