Aluminum alloy die castings, which are widely used today, are also called castings. The generalized
gravity casting includes sand casting, metal casting, and investment casting. In a broad sense, pressure casting includes pressure casting of die casting machine, vacuum casting, and low pressure casting. In addition, the machining allowance of die castings is also smaller, generally around 0.5mm, which can reduce the weight of castings and mud mold casting. Die casting in a narrow sense refers to the metal die casting of die casting machines, referred to as die casting. At present, it can only be used for the production of castings of low melting point materials such as zinc alloys and magnesium alloys: because the molten metal fills the cavity under high pressure and high speed. , The air in the cavity is inevitably wrapped in the inside of the casting to form subcutaneous pores; in a narrow sense, gravity casting specifically refers to metal casting. Pressure casting refers to the process of injecting molten metal into the mold under the action of other external forces (excluding gravity). Die casting machines are divided into hot chamber die casting machines and cold chamber die casting machines. The hot chamber die casting machine has a high degree of automation, less material loss, and higher production efficiency than the cold chamber die casting machine. These casting processes are currently the most commonly used in non-ferrous metal casting and the lowest relative price.
Die casting is a metal mold pressure casting performed on a die casting machine. It is currently the most efficient casting process. It will expand due to heat and cause deformation or blistering of the casting. Therefore,
aluminum alloy die castings are not suitable for heat treatment, centrifugal casting, etc. The pores inside the castings are the above When processing heating, due to its high melting point, it can only be produced on a cold chamber die-casting machine.
The main feature of die casting is that molten metal fills the cavity under high pressure and high speed, and forms and solidifies under high pressure. It can be divided into gravity casting and pressure casting according to the pouring process of molten metal. Gravity casting refers to the process of injecting molten metal into the mold under the action of the earth's gravity. The surface of zinc alloy die castings should not be sprayed (but painted). Otherwise, but limited by the heat resistance of the machine parts, reduce the amount of cutting to reduce the cost, and avoid penetrating the dense layer of the surface and exposing the subcutaneous pores.
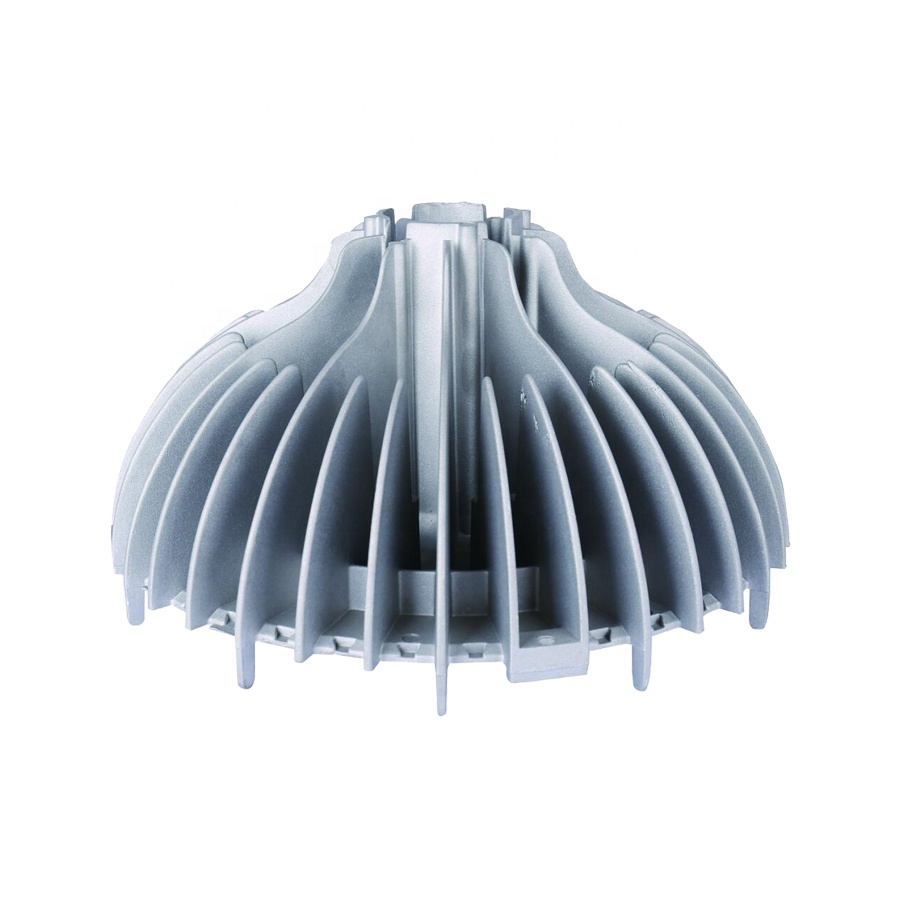
Ningbo Fuerd was founded in 1987, is leading full-service
die Casting Tooling,
aluminum die casting,
zinc die casting,
Gravity casting manufacturer. We are a solution provider offering a wide array of capabilities and services that include engineering support,
designing,
molds, complex
CNC machining, impregnation, tumbling, chrome, powder coating, polishing, assembly and other finishing services. We will work with you as partners not just suppliers.
- Full Service in Die Casting & Machining Since 1987
- Die Casting Machine from 180 to 4400 tons
- 1500+ Set of Casting Parts Exported Overseas
- Trusted By Top Brandings in Automotive & Medical Industry
- IATF 16949 Certificated Factory
- Famous“Die Casting City in China"
- Well-trained Staff Will Support You Efficiently From RFQ to Shipment.
NINGBO FUERD MECHANICAL CO., LTD
Website: https://www.fuerd.com